Georges Guiochon pointed out in his excelent reivew about monolithic stationary phases four directions from which we can expect a serious improvement in (monolithic) columns performance.
High temperature chromatography
High temperature chromatography, which causes a reduction in the viscosity of the mobile phase. So far, monolithic stationary phases have not yet been used at high temperatures but this is only a matter of time. High temperature liquid chromatography currently pioneered by Peter Carr and his group is going to be one of the major research areas in analytical chemistry for the next ten years. A significant reduction of analyses times by a factor between 3 and 4 is quite likely.
Increase in the pressure
An increase in the maximum pressure available to the analyst. Most commercial instruments can operate at inlet pressures of up to 40 – 50 MPa. A few of them can reach inlet pressures of 100 – 120 MPa and pumps able to reach 900 MPa are available. The use of high pressures requires far more caution than chromatographers are used to apply. This may create new, some times unexpected, safety hazards against which analysts should be forewarned. One advantage of monolithic columns is that extremely efficient columns, able to generate one or even several millions of theoretical plates could be operated with conventional HPLC instruments if long enough columns could be prepared.
Optimize the structure
A decrease in the minimum value of the height equivalent to theoretical plate (HETP) of the columns used. This will come from a reduction of the heterogeneity of the radial distribution of the flow-through pore sizes, also from a reduction of the average size of the domains of the monolithic column used and from a reduction in the variance of the domain sizes.
We have to be able to control (and suppress) monolith heterogeneity. My small prediction: one who is able to prepare the (monolithic) stationary phase with no or limited heterogeneity will be able to achieve unimaginable efficiency and column performance. Like for example homogeneous pillars.
Higher column permeability
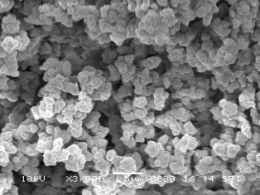
An increase in the column permeability. This requires an increase in the average flow-through pore size. Since this size is included in the domain size, this requirement is in conflict with the previous one. Both can be achieved only by decreasing the average size of the porons, which would increase the external and total column porosity at the expense of the internal column porosity and the total surface area of adsorbent in the column. There is no clear limit here but it does not seem that much can be gained. Most probably, a reduction in the variance of the domain size accompanied by an increase in the degree of radial homogeneity of the monoliths constitute the most promising avenues for the monolith designers and makers.
Solutions?
One of the possible ways how to connect these last two conflicting requirements can be preparation and optimization of hypercrosslinked monolithic stationary phases. The porous structure (flow through pores) can be optimized independently on the structure of the thin hypercrosslinked layer prepared on the surface of the monolith (micro- and mesopores). Firstly, the generic monolith is prepared (flow through pores) and then the surface of the stationary phase is modified with the hypercrosslinking reaction and thin layer of small pores is formed. Then, only the general models connecting the preparation and modification of the hypercrossllinked monoliths with their chromatographic properties have to be developed and understand.
What do you think about these suggestions?
PS: if you haven’t done yet – look at the review written by Georges Guiochon. There is all you need to know about monoliths but were afraid to ask.