Many applications of porous materials in areas such as catalysis, adsorption, ion exchange, chromatography, and solid phase synthesis rely on the intimate contact with a surface that supports the active sites.
In order to obtain large surface area, a significant number of smaller pores should be incorporated into the polymer.
Types of pores
The most substantial contribution to the overall surface area comes from micropores, with sizes smaller than 2 nm, followed by the mesopores ranging from 2 to 50 nm [1,2]. Larger pores (macropores) contribute very little to the surface area. However, these pores are essential to allow liquid to flow through the material at a reasonably low pressure. This pressure, in turn, depends on the overall porous properties of the material [3].
From those kinds of pores, there are two main types in porous structure of monolith:
- the through pores enabling an easy flow of the mobile phase and
- the mesopores filled with the “stagnant” mobile phase in which the solute molecules should migrate to access the active adsorption sites.
The volume of the mesopores and the morphology of the mesopore space significantly affect the mass transfer resistance and hence the chromatographic band broadening. It also controls the phase ratio in the column and may influence the hydrophobicity of the monolithic material and the retention properties [4].
Therefore, the pore size distribution of the monolith must be adjusted properly to fit each type application. Important parameters such as temperature, composition of the pore-forming solvent mixture, and content of crosslinking monomer allow the tuning of the average pore size within a broad range, from tens to thousands of nanometres [3,5,6].
Temperature
The effect of temperature on the kinetics of polymerization allows the preparation of macroporous polymers with different pore size distributions from a single composition of the polymerization mixture. The effect of temperature can be readily explained in terms of the nucleation rates, and the shift in pore size distribution induced by changes in the polymerization temperature can be explained by the difference in the number of nuclei that result from these changes [3,6]. With higher temperature, monoliths with smaller pores are prepared.
Pore-forming solvents
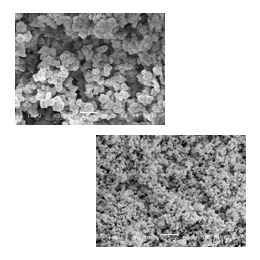
The choice of pore-forming solvent (porogen) is the mostly used tool for the control of porous properties without changing the chemical composition of the final monolith. In general, larger pores are obtained in a poorer solvent due to an earlier onset of phase separation. The porogenic solvent controls the porous properties of the monolith through the solvation of the polymer chains in the reaction medium during the early stages of the polymerization [3,5].
Properties of pore-forming solvents
Specific attention was paid to the design of the porogen mixtures for preparation of methacrylate monolithic columns. Ideally, this system should provide:
- preparation of a homogenous, single phase polymerization mixture from a charged, water soluble monomer and hydrophobic monomers;
- direct uniform incorporation of these monomers with widely differing polarities into a macroporous polymer monolith;
- exact control of the porosities of the monolithic material over a broad range; and finally
- facile initial washing and equilibration of the capillary column.
Extensive studies led to the development of a ternary porogen solvent system consisting of water, 1-propanol, and 1,4-butanediol in various proportions [7]. Besides the traditional ternary mixture binary porogenic solvents with only alcohols have also been adopted. Compared with ternary porogenic solvents, the design with binary ones allows for fine control of the pore size and tailoring of the specific surface area of the monolithic polymers. Monoliths prepared with binary porogenic solvents have a different pore distribution from those prepared with ternary porogenic solvents – with larger surface area and containing more of the small pores [8].
Cross-linker
In contrast, increasing the proportion of the cross-linking agent present in the monomer mixture affects the chemical composition of the final monoliths. At the same time, it also decreases their average pore size as results of early formation of highly cross-linked globules with a reduced tendency of coalesce. The experimental results imply that, in this case, the pore size distribution is controlled by limitations in swelling of cross-linked nuclei [3].
The control of porous properties of the organic polymer monolithic materials is a complex process influenced by various parameters.
References
- K.K. Unger, Porous silica, J. Chromatogr. Library, 16, 1979, Elsevier, p. 15.
- IUPAC, Manual of Symbols and Terminology, Apendix 2, Part I, Colloid and Surface Chemistry, Pure Appl. Chem., 31 (1972) 578.
- C. Viklund, F. Svec, J.M.J. Frechet, U. Irgum, Chem. Mater, 8 (1996) 744.
- D. Moravcová, P. Jandera, J. Urban, J. Planeta, J. Sep. Sci., 23 (2003) 1005.
- B.P. Santora, M.R. Gagne, K.G. Moloy, N.S. Radu, Macromolecules, 34 (2001) 658.
- F. Svec, J.M.J. Frechet, Macromolecules, 28 (1995) 7580.
- E.C. Peters, M. Petro, F. Svec, J.M.J. Frechet, Anal. Chem., 69 (1997) 3646.
- L. Zhang, G. Ping, L. Zhang, W. Zhang, Y. Zhang, J. Sep. Sci., 26 (2003) 331.